• Precision PCB Assembly:
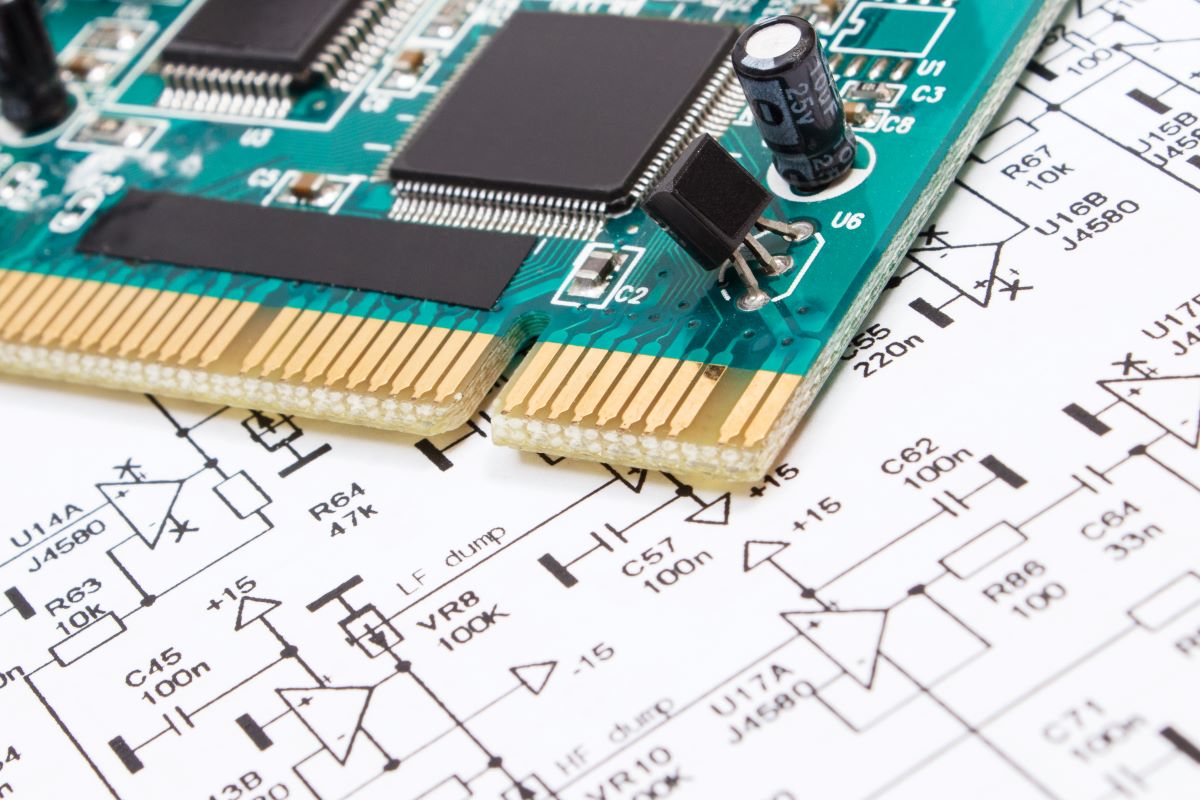
As the foundation of modern electronics, the modern printed circuit board (PCB) is a highly precise piece of technology.
However, precision in PCB assembly doesn’t just mean fitting small components onto ever-evolving substrates to facilitate the steady march of progress.
It means maximizing efficiency, eliminating costly errors, and meeting the flexible needs of customers.
When it comes to choosing a PCB assembly partner, finding one that combines precise high-end technology with robust quality standards and excellent customer service can be an invaluable competitive advantage.
In the sections ahead, we’ll explain the full process of PCB assembly and where precision fits into the equation to help electronics manufacturers understand what precision in PCB assembly truly means.
What is PCB Assembly?
At its core, PCB assembly is a process of mounting useful electronic components onto a substrate, usually made of a composite fiberglass material (FR4), to create a functional circuit.
Since it involves the precise placement of many small pieces, modern PCB assembly is a highly complex task that requires extensive knowledge and access to advanced technology.
The fundamental aspects of PCB production can be broadly categorized into three distinct stages:
1. Pre-Assembly: Design, and Substrate Procurement
PCB assemblers typically obtain substrate materials like FR4 through dedicated materials manufacturers. They take into consideration things like size, layer count, and thickness.
Then, a design schematic is created, which includes details such as the components needed as well as traces, vias, and other features important for the reliability and functionality of the device.
Finally, the PCB layout is transferred onto the substrate through a process known as etching. Tiny holes, known as vias, may also be drilled into the board. These processes create the physical pathways necessary to form electric connections between components.
2. Assembly: Component Placement and Soldering
Here is the core of the assembly process, where electronic components are mounted and a functional circuit is created on the board.
It begins with solder paste, a compound of flux and solder particles that prepare the surface for component placement.
Components are then placed into their specified positions using automated machines known as pick-and-place machines. Surface mount technology (SMT) and through-hole technology (THT) are two common techniques used to place components on modern boards.
Finally, components are permanently attached to the board through soldering. Depending on the components and how the board is designed, different processes like reflow soldering or wave soldering may be used to form these permanent connections.
3.Post-Assembly: Inspection and Quality Testing
In the final stage, PCBs are assessed to ensure they meet all specifications and quality standards.
This is traditionally done through a combination of automated processes, such as automated optical inspections (AOI), as well as tool-assisted manual inspections like x-ray inspections.
Assembled PCBs are then powered on and tested for functionality. This also involves dedicated machines that simulate operating conditions and long-term usage, ensuring the boards will stand the test of time.
If necessary, boards may undergo a rework at this stage, but assuming the board meets standards, it is ready to be packed and shipped to the customer.
The Precision Factor in PCB Assembly
As electronic devices have become increasingly compact, with higher demand for robust operational tolerances, the complexity of PCB assembly has risen dramatically. Modern PCB assembly requires the utmost precision achievable only through advanced technologies.
Balancing Precision with Efficiency
The placement of fine-pitch components often requires extremely small distances between pins. Misalignment, even by a fraction of a millimeter, can result in short circuits and a malfunctioning board.
On top of this demand for precision, boards need to be mass-producible. Creating hundreds or even thousands of boards on a short timescale necessitates automation. PCB assemblers utilize machinery equipped with cameras, advanced vision systems, and laser technology to ensure accurate alignment.
Dealing with Multi-Layer PCBs
Today’s PCBs can have dozens of layers that each require precise alignment. Mistakes here can disrupt electrical connections between layers and compromise the board’s functionality.
To ensure alignment before layers are laminated together, PCB assemblers make use of AOI to check for defects on each layer.
The Implementation of HDI Technology
High-Density Interconnect (HDI) PCBs are boards with a high density of components. These boards require advanced HDI-specific technology to assemble.
HDI includes a mixture of PCB design software and manufacturing machines that place vias, route traces, and secure components in a compact formation without errors.
How PCB Assemblers Use Technology to Achieve Cost-Effective Precision
A lack of precision in PCB assembly doesn’t just limit the device’s functionality, it can also lead to many problems, from electrical shorts to wasted resources. Faulty boards and malfunctioning devices can cause a loss of trust from customers, ultimately compromising the business who created them.
To meet the ever-increasing demands for precision in PCB assembly, modern manufacturers make use of a combination of cutting-edge hardware and sophisticated software technologies.
These advancements not only enhance precision but also contribute to a more cost-effective assembly process.
Cutting-Edge Hardware
- Automated Machines and Robots
Everything from material handling to component creation to pick and place can be made easier through automated machines and robots.
These can reduce labor costs, eliminate waste, and accurately identify assembly faults. AI-based robots offer precise automation as well as deep insights that can help optimize the entire assembly operation.
- 3D X-ray Inspection Systems
X-Ray technology provides a non-destructive way of checking for defects beneath the surface of a multi-layer PCB.
It allows for the detection of problems that would be otherwise invisible to the naked eye or even AOI systems, providing indispensable and precise assurance of the integrity of connections within densely packed PCBs.
- Solder Paste Inspection (SPI) Systems
SPI technology uses laser or optical systems to measure the volume, area, and shape of solder paste, ensuring precision before the placement of components.
This adds precision and efficiency to the soldering process, minimizing the risk of cold-solders, bridging, insufficient solder, or tombstoning—a defect wherein a bipolar surface mount component partially lifts off the PCB.
Sophisticated Software
- Simulation Technologies
Simulations of PCB performance can be utilized to plan PCB circuit layouts. Simulations help predict potential issues with the PCB design, ensuring design engineers can optimize the layout and maximize efficiency before the production process begins.
- Cloud-Based Data Management
IoT-connected machines and AI robots collect a vast amount of data during assembly, which can be stored in the cloud. Making this data accessible for analysis improves the production process and product quality by enabling assemblers to leverage insights for everything from process optimization to predictive maintenance.
- AI Fault Detection
AI algorithms are increasingly used to identify defects and help optimize the PCB production process. Through machine learning, these systems can accurately identify faults in soldering or component placement and even be used to suggest improvements by analyzing data from the production line.
PCB Quality Control and Standards
Adherence to industry standards plays a big role in the manufacture of precision PCBs. They help customers and manufacturers understand benchmarks for the consistency, reliability, and performance of electronic devices.
Standards like IPC, IEEE, and ISO, listed below, don’t just help guarantee the quality of PCBs but can give electronics manufacturers who look for them a competitive advantage in the global market:
IPC Standards
- IPC-A-610: The gold standard for PCB assembly quality. A-610 outlines the criteria for soldering quality, component placement accuracy, and more.
- IPC-6012: Includes specifications for rigid PCBs, including structural integrity, conductor spacing, and electrical properties.
- IPC-7711/7721: Offers guidelines to ensure that PCBs maintain high levels of precision even after modification.
AS9100/ISO9001
AS9100/ISO9001 is a globally recognized standard for quality management.
While not specific to electronics manufacturing, ISO 9001 certification demonstrates a company’s commitment to ensuring quality and continuous improvement in its processes, including PCB assembly.
IEEE Standards
IEEE provides guidelines for the design, testing, and implementation of electronic circuits. While more technical and specific in nature, they help manufacturers and customers ensure the precision and functionality of electronic systems.
The Business Impact of Precision PCB Assembly
Modern PCB assemblers are able to manufacture boards that are smaller, more flexible, more compact, and more versatile than ever before.
However, all of this precision isn’t just for show.
For electronics manufacturers who rely on high-quality devices that will withstand regular use by their consumers, faulty PCBs can pose a significant business risk.
Recalls Can Cost a Fortune and a Reputation
Product recalls can be extremely costly. Consider these recent recalls from the auto industry:
- In September 2022, Kia recalled more than 70,000 cars due to faulty PCBs.
- Tesla is currently in the process of issuing a software update to more than 2 million of its electric vehicles, which is designed to overcome a hardware shortcoming.
- In 2022, Cummins was forced to issue a recall of 12,196 engines because of a faulty PCB within the engine control module (ECM).
In each of these cases, the faults in the electronic systems made the vehicles more dangerous to operate, potentially costing lives in addition to the resources required to complete the recall repairs.
Precision manufacturing is all about avoiding problems like these. They not only make products more efficient and safer but also reduce the risk of critical malfunctions that manufacturers often have to scramble to fix.
Precision = Profit
The more precisely a manufacturer can place components, the more complex their final product can be. However, increased precision also means reducing the likelihood of errors. This combination of increased complexity and efficiency is at the heart of why high precision is so important in the world of PCB assembly.
- For Manufacturers: Precision means reduced error rates, improved yield, enhanced product quality, and the enablement of innovation and miniaturization. All of these factors contribute to a brand’s reputation and customer loyalty.
For Customers: High precision means reliability, performance, longevity, and customization. Modern electronics manufacturers have a never-ending demand for more complex products, but they need them actually to work. Precision means staying balanced along the cutting edge.
Choosing the Right PCB Assembly Partner
Selecting a PCB assembler that meets high standards for precision is essential for ensuring the reliability and performance of your product.
Consider each of these factors carefully before choosing your assembly partner:
Certifications and Quality Control
The standards we listed above exist for a reason—they’re here to help consumers ensure the manufacturing partners they choose to work with are committed to quality and performance standards.
Some standards, like ISO 9001 and IPC A-610, apply generally to any PCB manufacturer, but those working within niche industries (such as aerospace, automotive, or medical devices) will want to check for additional certifications from their PCB assembler.
Technology
To facilitate a wide range of products with a reasonable turnaround time and a high standard of quality, PCB assemblers should have access to state-of-the-art technology and equipment.
Ask the assembler you’re thinking of working with to tour their facilities, if possible, and ask for a list of available manufacturing techniques to ensure they can handle anything you throw at them.
Vision and Communication
Aside from the physical ability to produce any board you need, perhaps the most important factor to consider is whether the PCB assembler understands your vision and aligns with your values.
Look for a PCB assembler who makes an active effort to work alongside you in the design process, keep you updated throughout the production, and get back to you quickly when you have questions or concerns.
Ultimately, you should seek to form a partnership with your PCB assembler—one focused on mutual growth and collaboration. Having a reliable source of high-quality PCBs means you can focus on creating the next generation of high-performance devices rather than worrying if you have the technology to keep up with your imagination.
Imagineering is Ready to Assemble Your Next PCB
Precision in PCB assembly is about more than just placing tiny components onto increasingly compact substrates.
It means staying in touch with the latest developments in hardware and software, keeping rigorous industry certifications, improving efficiency and quality simultaneously, and helping customers realize their vision for their new electronic products.
Since 1986, Imagineering has been combining cutting-edge technology with best-in-class service to produce high-quality printed circuit boards for more than 30,000 customers.
We have the technology, expertise, and vision to help make your latest electronic design a reality.
Your next PCB assembly partner is here. Contact Imagineering today, and together, we’ll build the next generation of electronics.